http://www.amphibiagroup.com/single-post/2016/11/25/Environmental-and-structural-benefits-of-using-Engineered-bamboo-products-EBPs
Environmental and structural benefits of using Engineered bamboo products (EBPs)
November 25, 2016
|
Amphibia BASE
Bamboo can be engineered to form products with improved and/or standardised mechanical, physical and aesthetic properties. As in the case for other lignocellulosic materials such as wood, bamboo poles (culms) with variable diameters, lengths and shapes can be transformed into straight edged engineered products with predictable properties for construction applications.
Engineered bamboo products (EBPs) and engineered wood products (EWPs) possess an intrinsic carbon storage capability, as well as potentially lower embodied energy and carbon dioxide emissions from manufacturing than conventional construction products such as concrete or steel. For instance, the carbon footprint of concrete and stainless steel (304) is about twice to ten times higher than that of a bamboo plywood (a laminated EBP) or an indoor use plywood according to IDEMAT database (2016) [1]. Seemingly, the embodied energy for producing one kilogramme (kg) of stainless steel is almost four times higher than that of producing one kilogramme of plywood [2] or bamboo plywood; this is 56.70 MJ/kg for the former and 15 MJ/kg and 15.5 for the laminated EBP [1]. Figure 1 illustrates EBP's capability of storing more carbon dioxide (CO2) than the raw and non-processed bamboo culms. This is, more CO2 storage equivalent in the bamboo plantation due to the higher use of material per dry weight (d.w.) for the manufacture of EBPs.
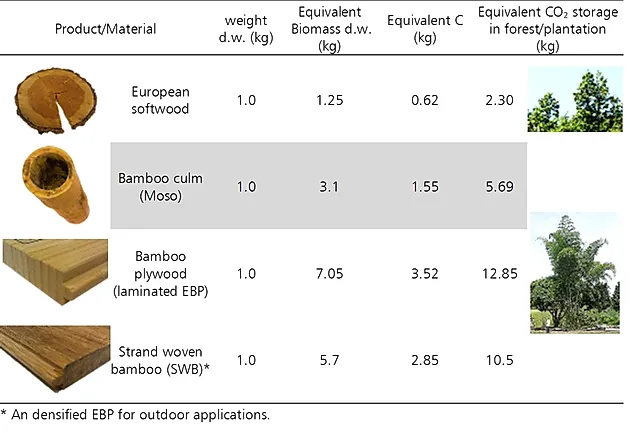
Figure 1 Equivalent C02 sequestration in bamboo and wood forest for different bamboo based products. Data from [3].
In addition to bamboo’s remarkable environmental features and high yield of carbon storing biomass when transformed into durable EBPs, recent research at the University of Bath (UK) has demonstrated their potential as a complementary to wood material (not a substitute) in structural applications [3]. Cross laminated Guadua-bamboo (G-XLam) panels (Figure 2) developed and tested at this university with the support of British firm Amphibia BASE showcased an approximate two-fold increase in density and MOE when compared to analogous cross laminated (CLT) panels (M1 BSP crossplan by Mayr-Melnhof Holz) (Table 1). This is, the in-plane compression moduli of elasticity of these CLT panels in the main direction (Epc,0) and transverse direction (Epc,90) were about half of that of G-XLam3 and G-XLam5 panels (three and five layers); e.g. Epc,0 was 7.57GPa and 14.83 GPa for CLT3 and G-XLam3 panels.
Figure 2 G-XLam bamboo-Guadua panels for stiffness driven applications
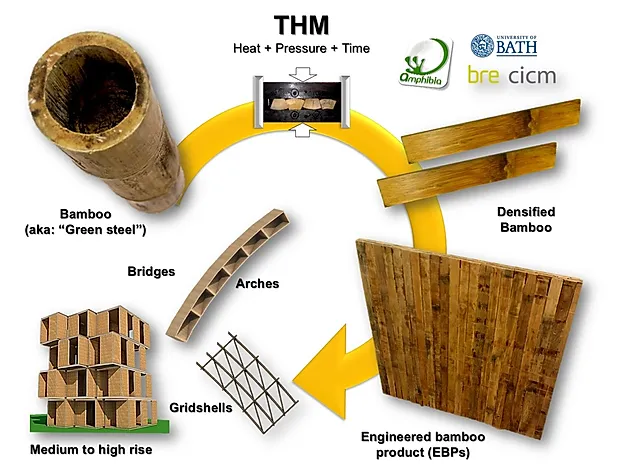
Table 1 Summary of the results obtained from the in-plane compression panel testing and the FE and predicted values previously obtained by [4]
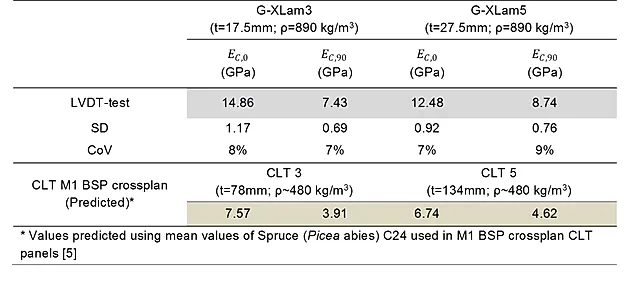
On the other hand, the thickness of G-XLam3 and G-XLam5 panels is almost a fifth of CLT3 and CLT5 panels (e.g. thicknesses of CLT5 and G-XLam5 were 134mm and 27.5mm, respectively). This is a desirable feature stiffness driven design but, G-XLam panels possess a high slenderness ration, which presents a structural challenge in overcoming buckling. Nevertheless, potential engineering applications for G-XLam panels are sandwich panels and stressed skin structures (e.g. monocoque), where thin but very stiff layers are separated by a core or internal structure that increases the second moment of area and reduces buckling. EBPs such as these G-XLam panels open a whole new approach to the use of bamboo in structural applications, where bamboo is not seen as substitute but in combination with wood and/or lightweight cores to provide the required stiffness with reduced cross-sections. However, further testing, research and understanding of the mechanical behaviour of EBPs is required, together with the optimisation of current manufacturing processes and their incorporation within timber standards for structural design.
Overall, EBPs such as G-XLam and the commercially available bamboo plywood and strand woven bamboo (SWB), whose physical (e.g. density, durability, hardness) and mechanical properties have been improved through industrial processes outperform conventional materials in terms of their contribution to the overall CO2 sequestration. Additionally, EBPs store more CO2 than non-processed bamboo culms.
More information about engineered bamboo products (EBPs) can be found at https://goo.gl/sRGNa9 [6]
References
[1] Delft University of Technology, “IDEMAT database.” Faculty of Design, Engineering and Production, Delft, 2016.
[2] G. P. Hammond and C. I. Jones, “Embodied energy and carbon in construction materials,” Proceedings of the Institution of Civil Engineers - Energy, vol. 161, pp. 87–98, 2008.
[3] H. F. Archila, “Thermo-hydro-mechanically modified cross-laminated Guadua-bamboo panels,” PhD Thesis, University of Bath, 2015.
Also published at ICE Designing Buildings Wiki
沒有留言:
張貼留言